Prototyping Material Flow for R&D Fabrications
Situation
A North American research and development facility of a U.S. based market-leading manufacturer of commercial jetliners and defense, space and security systems, fabricates prototypes for the purpose of testing and validation. Parts are produced in limited numbers throughout the fabricating shop. The component finishing process involves both hand sanding of composite materials and coatings applications that are required on an intermittent basis and performed “in-place” and without an enclosure. After each sanding operation, composite dust settled throughout the entire facility requiring periodical cleaning of the entire shop floor at a cost of tens of thousands of dollars per cleaning. In addition, the coatings process required a paint arrestor for improved results. A permanent enclosure was not a viable solution due to the need to work "in-place" and the cost-prohibitive requirement for air makeup. A permanent enclosure would also reduce the usable existing floor space of the R&D facility.
Solution
Duroair suggested the use of a unique prep room design that includes its patented, fully portable, non-vented DuroPure™ indoor air purification system equipped with self-cleaning dust filters and a dust collection system, in combination with a custom-designed DuroRoom™ retractable enclosure. The hybrid DuroPure™ unit and the dust collector provides both air handling and dust filtration/collection, while DuroPure™'s patented Taper Draft Airflow Technology improves drying times and optimizes overspray control during the coatings application. As an added benefit, the DuroRoom™ enclosure retracts to 20% of the extended length, maximizing shop floor space when not in use.
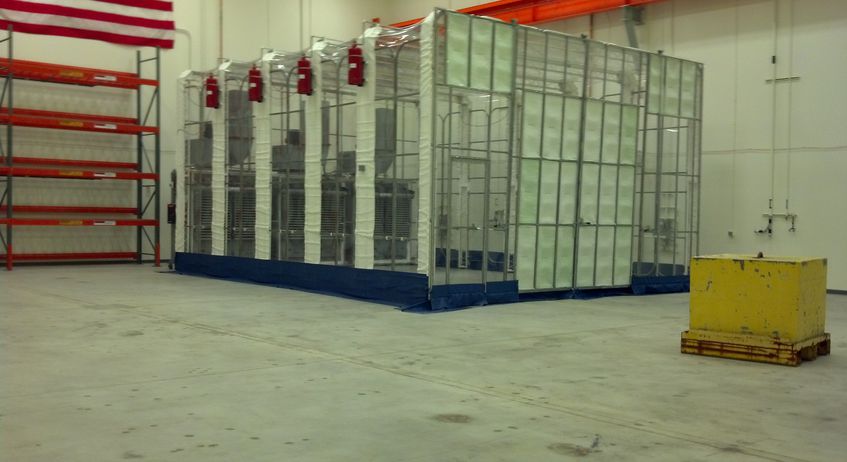
Results
The result of this solution is enhanced efficiency of material flow by installing the retracted Duroair prep room around the workpiece prior to the sanding and coating stages. Dust is effectively and cost-efficiently filtered and collected while the coating quality is optimized. The use of existing floor space is maximized. The investment in the Duroair prep room was recovered in just a few dust cleaning cycles and there were no equipment and installation costs for air makeup.