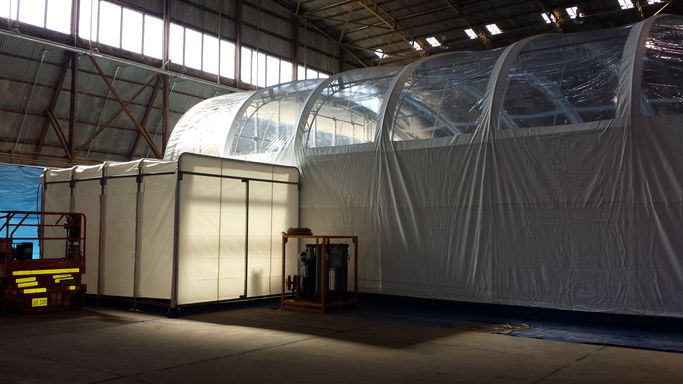
Modular Clean Room Design For Manufacturing Flexibility
Ensuring quality control while balancing long-term construction with short-term cutting, welding, or surface prep and spraying tasks is an ongoing logistical challenge. Navigating these cellular workflows is critical for aerospace OEMs, ship and boat manufacturers, and for operations conducting prototyping and R&D.
How do you cost-effectively isolate manufacturing processes to keep damaging elements out and clean air around each workpiece?
Contact UsBring Compliant Clean Air to On-Demand Work Spaces
Duroair’s retractable clean rooms create clean air environments wherever they are needed. We combine our DuroRoom™ retractable enclosure with our DuroClean™ engineered exhaust system into one flexible, cost-effective solution for portable clean rooms and isolation rooms.
Duroair modular clean rooms can be placed anywhere in a manufacturing facility without having to install supplementary ductwork — or pay for ongoing air make-up costs. Our portable, retractable enclosures with non-vented air filtration can be engineered for large or small self-contained work environments, wherever and whenever needed.
Whether isolating a manufacturing process from the larger work environment (negative pressure) or protecting a process from contamination (positive pressure), our DuroRoom™ and engineered filtration systems help guarantee worker safety from toxic dust and fumes, while reducing operating expenses and increasing productivity.
Benefits of Duroair’s custom portable clean room design includes:
- Increased workflow efficiency for stop-and-start R&D processes
- Reduced material handling by not having to transport large workpieces to a dedicated clean air space
- Eliminated need for expensive equipment and installation for air make-up
- Laminar or turbulent airflow as required
- Unsurpassed control of isolated work environments, including pressure (positive or negative), humidity, and temperature air flow patterns, and harmful dust particulates and gaseous contaminants
Technical Specifications
- Protection to ISO level 6
- HEPA filtration 99.97% capture rate
- Filtration capable of capturing hexavalent chromium superior to NESHAP 319
- Positive or negative pressure as required
- Temperature and humidity control
- Air quality monitor and magnehelic gauge to indicate when filters require changing
- NFPA 33 compliant motor and electrical systems work outside of the air stream
- Air filtration ranging from 800 CFM to 80,000 CFM
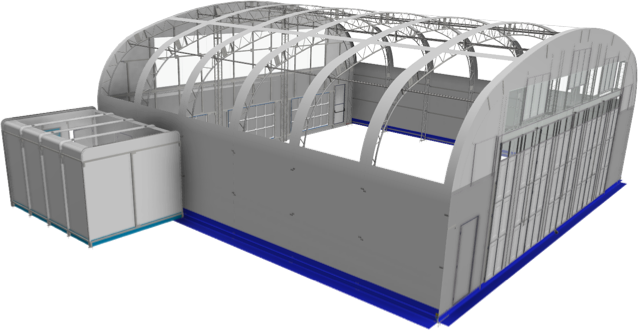
Clean Air Code Compliance
Code Compliance | Code Description |
---|---|
NFPA 33 | spray application |
ANSI Z9.7 | per the requirements of NFPA33 Chapter 7.5.2. |
NFPA 17 | dry chemical extinguishing systems |
NFPA 18 | spray application operations in membrane enclosures for fire suppression |
NFPA 701 | fabric flame resistance |
OSHA | silica standard for general industry |
OSHA 29CFR – 1910.107 | spray finishing |
OSHA 29CFR – 1910.94 | ventilation |
OHSA O.Reg 851-63 | ignition or explosive |
OHSA O.Reg 851-65 | dust – ignition or explosive |
OHSA O.Reg 213.5.12 | fire code – spray operation |
OSHA 29CFR – 1910.107 | spray finishing using flammable and combustible material |
EPA 40CFR – Part 63.11173 | spray finishing requirements (Electrical CSA Certified) |
NESHAP | National Emission Standards for Hazardous Air Pollutants |
UL | (U.S. and Canada) |
ISO Cleanroom compliant | up to Class 1000/ISO6 (ISO class clean room typically measures micron sizes 5.0µ, 0.5µ and 0.3µ) |