The ROI of Mitigating Hexavalent Chromium Exposure
In a recent blog, we looked at serious health hazards and bottom-line risks from occupational exposures to hexavalent chromium in metal fabrication and manufacturing. Fortunately, there are cost-effective, clean air solutions to safeguard employees, increase overall productivity, and profits.
Duroair’s industrial air filtration systems isolate and capture dangerous hexavalent chromium particulates and other volatile organic compounds. Below are a few examples of how this technology can improve operational processes and overall profitability.
Decrease Downtime
If employees become too ill to work, downtime is inevitable. Traditional methods to safeguard workers can also result in lost uptime. For many aerospace and aviation manufacturers, meeting OSHA’s Permissible Exposure Limit (PEL) requires opening all hangar doors during sanding and painting to release the hexavalent chromium particulates when parts or planes cannot be moved into a traditional paint booth.
This means all other manufacturing processes go on hold until these tasks are complete. It can take several hours before workers are allowed to re-enter the building and get back to work.
With Duroair’s industrial air filtration systems, manufacturers can safely isolate painting and coating processes. These clean air solutions protect workers and prevent toxic volatile organic compounds from escaping the sanding/painting enclosure. Additional workflows proceed unimpeded, and there’s no need for workers to spend hours in a break room waiting for dangerous toxins to vent outside.
Improve Productivity
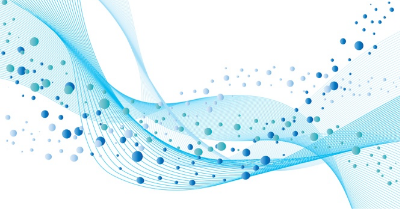
Duroair's patented Taper Draft Airflow Technology prevents dust and hex chromate particulates from settling on workpieces or the shop floor.
Duroair’s systems are also equipped with Taper Draft Airflow Technology that pulls hex chromate particles and dust directly into the air filtration chamber, so the particulates don’t settle on the workpiece or the shop floor. Employees don’t have to waste valuable man-hours cleaning dirty floors and repairing dust-clogged machinery. This also speeds drying times for water-based paints and coatings, without the use of additional quick-dry agents.
Reduce Material Handling
For MRO tasks involving large aircraft, submarine, or other bulky metal pieces, preventing occupational exposures to hexavalent chromium often requires extensive material handling to move assemblies into and out of dedicated clean air enclosures. But, what if you could bring clean air to each workpiece?
Duroair combines custom non-vented air filtration systems and retractable enclosures to create self-contained work environments for helicopters, airplane assemblies, and other larger parts for sanding and painting.
This technology also eliminates the need to vent air-conditioned or heated air to release hex chromate particles and other volatile organic compounds. Duroair’s industrial air filtration system recirculates clean air back into the building without the need to use makeup air.
Expand Production Capability
PEL and OSHA limits how many times per year industrial facilities can vent hexavalent chromium particulates. But, without a process to isolate and capture all these particulates, manufacturers are limited to a specific number of sanding, coating, or painting processes per year to stay in compliance.
With Duroair’s six-stage filtration technology, 100% of the offending hex chromates are safely contained. This removes the number limitations for manufacturing processes and task consumables, such as chromium-based aluminum coatings and rust-prevention paints. Facilities can significantly increase their production capability without being handcuffed by regulatory requirements.
Guarantee Indoor Air Safety for True ROI
Compromised safety leads to a compromised bottom line. Even one workplace accident or serious illness due to hexavalent chromium exposure can risk thousands or even millions of dollars in legal fees and OSHA and EPA regulatory action.
But, with Duroair’s hexavalent chromium containment technology, manufacturers can protect their most valuable assets – their employees. This clean air technology goes beyond OSHA and NESHAP 319 requirements to cost-effectively mitigate health risks that drain profitability.
A safe workplace means employees can successfully complete critical tasks such as:
- Airplane repair and refurbishing
- Aircraft wing and component replacements
- Engine repair preparation
To learn how Duroair’s industrial air filtration systems can reduce hexavalent chromium safety risks while improving productivity, contact our industrial clean air experts today.